對(duì)于油氣管道來說,管道的承載能力取決于管道焊縫的焊接質(zhì)量,所以焊接質(zhì)量對(duì)于管道的安全運(yùn)行至關(guān)重要。油氣管道焊縫缺陷引發(fā)的泄漏事故可能造成嚴(yán)重安全風(fēng)險(xiǎn),因此對(duì)接焊縫檢測(cè)技術(shù)成為國內(nèi)外研究重點(diǎn)。電磁無損檢測(cè)憑借其非接觸、高效率、無損傷等優(yōu)勢(shì),已成為管道焊縫缺陷檢測(cè)的核心手段。
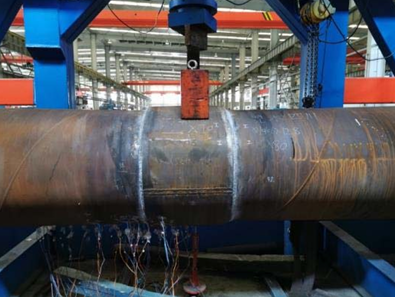
管道焊縫缺陷及缺陷類型
管道焊縫區(qū)域常出現(xiàn)兩類缺陷:表面可見的外部缺陷(如咬邊)和隱蔽性更強(qiáng)的內(nèi)部缺陷(包括裂紋、氣孔、夾渣等)。據(jù)統(tǒng)計(jì),全球油氣管道焊縫開裂事故中,80%以上的失效源于內(nèi)表面萌生的裂紋、未焊透、未熔合三類平面型缺陷,以及具有尖銳幾何特征的咬邊缺陷。
這類缺陷在管道內(nèi)壓波動(dòng)、溫度變化等交變載荷作用下,會(huì)形成顯著的應(yīng)力集中效應(yīng)。其應(yīng)力集中系數(shù)可達(dá)正常區(qū)域的3-5倍,導(dǎo)致缺陷尖端持續(xù)擴(kuò)展,最終使管體有效壁厚減少30%以上,嚴(yán)重威脅管道結(jié)構(gòu)安全及服役壽命。
管道焊縫缺陷檢測(cè)技術(shù)
目前實(shí)際應(yīng)用中主要包含四種技術(shù)路徑:渦流檢測(cè)、電磁超聲檢測(cè)、漏磁檢測(cè)及磁擾動(dòng)檢測(cè),這些方法在管道焊縫檢測(cè)中展現(xiàn)出良好的工程適用性。
渦流檢測(cè)
渦流檢測(cè)技術(shù)基于電磁感應(yīng)原理實(shí)現(xiàn)非接觸式探傷,其核心優(yōu)勢(shì)體現(xiàn)在以下三方面:首先,檢測(cè)過程無需物理耦合介質(zhì),且可穿透表面防腐層(厚度≤3mm)直接檢測(cè)基體缺陷,涂層對(duì)檢測(cè)靈敏度的影響率低于15%;其次,設(shè)備系統(tǒng)集成度較高,典型便攜式渦流儀重量不超過5kg,單次檢測(cè)能耗低于50W,作業(yè)過程無輻射污染源;第三,采集的阻抗平面信號(hào)可通過AD轉(zhuǎn)換模塊實(shí)現(xiàn)數(shù)字化(采樣率≥1MHz),結(jié)合小波降噪和神經(jīng)網(wǎng)絡(luò)算法,可使缺陷特征識(shí)別準(zhǔn)確率提升至92%以上,特別適用于長輸管道環(huán)焊縫的在線快速篩查。
渦流檢測(cè)原理示意
電磁超聲檢測(cè)
電磁超聲檢測(cè)技術(shù)適用于被測(cè)試件的深層次缺陷檢測(cè),對(duì)于表面或者近表面缺陷的檢測(cè)能力較弱。與其他超聲檢測(cè)方式相比,電磁超聲檢測(cè)技術(shù)具有換能效率較低、不能運(yùn)用于非金屬等局限性。
電磁超聲檢測(cè)原理示意
漏磁檢測(cè)
與其他檢測(cè)方式相比,漏磁檢測(cè)技術(shù)易實(shí)現(xiàn)自動(dòng)化,適合組成自動(dòng)檢測(cè)系統(tǒng),且信號(hào)可從傳感器直接傳遞到計(jì)算機(jī),減少了人為因素的影響,提高了檢測(cè)精度,有較高的可靠性。
漏磁檢測(cè)技術(shù)原理及流程
磁擾動(dòng)檢測(cè)
磁擾動(dòng)是一種常見的電磁場(chǎng)物理現(xiàn)象,是伴隨著磁擾動(dòng)引起的磁重構(gòu)和重聯(lián)產(chǎn)生的新的磁場(chǎng)變化。磁擾動(dòng)檢測(cè)技術(shù)主要檢測(cè)結(jié)構(gòu)包括永磁體、漆包線和被測(cè)試件。
磁擾動(dòng)檢測(cè)原理及流程
結(jié)語
在油氣管道對(duì)接焊縫電磁無檢測(cè)損技術(shù)的發(fā)展進(jìn)程中,諸多研究呈現(xiàn)出相輔相成的關(guān)系。將多種電磁檢測(cè)方式相互組合應(yīng)用,既能提升檢測(cè)精準(zhǔn)性,又能克服單一檢測(cè)技術(shù)存在的局限。隨著對(duì)電磁檢測(cè)技術(shù)研究的持續(xù)深入,管線焊縫檢測(cè)技術(shù)有望開辟更為廣闊的發(fā)展空間。